Bulk Material Handling: Transforming Industries with Efficiency
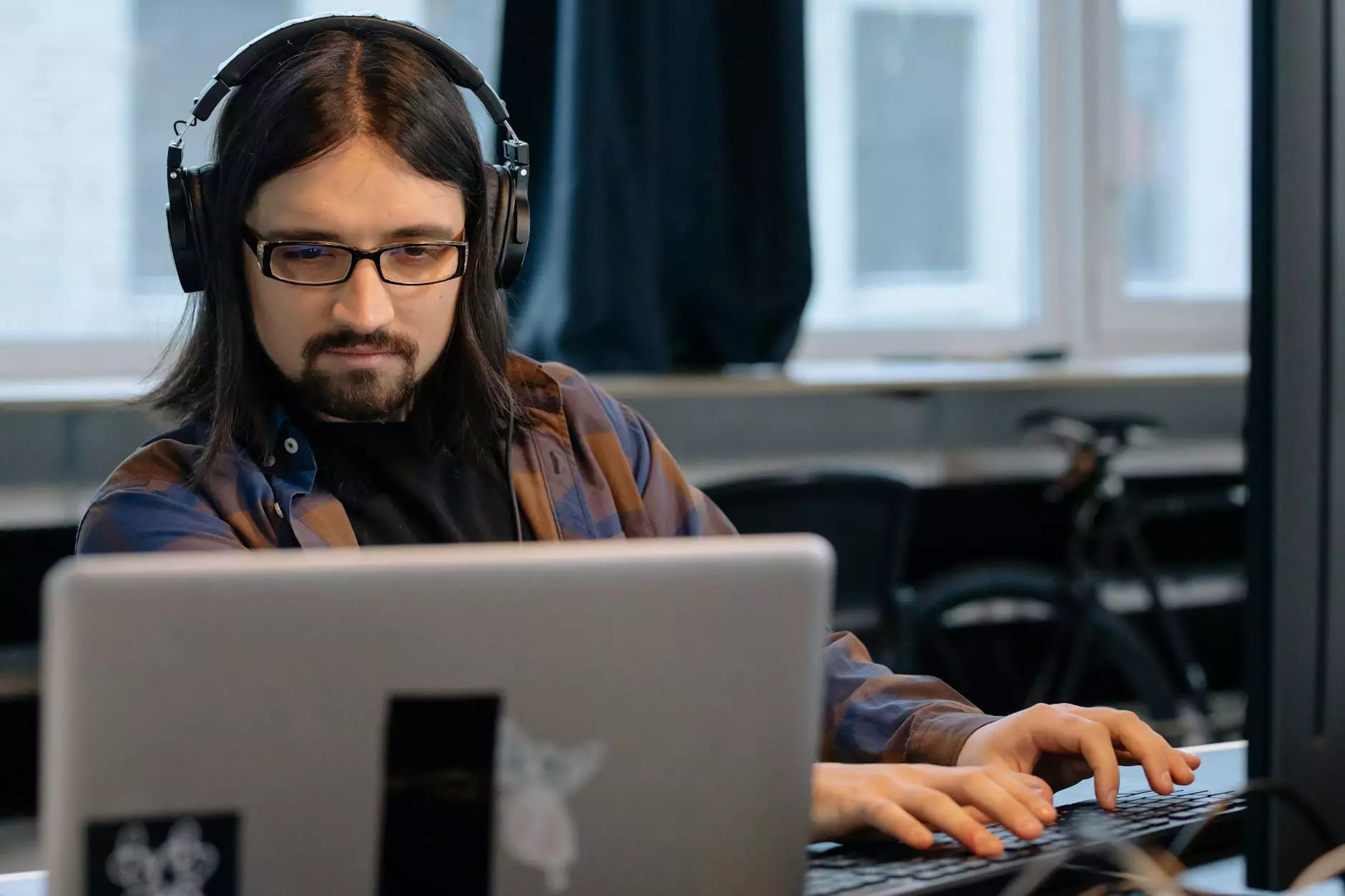
In the ever-evolving landscape of global industries, bulk material handling has emerged as a crucial component impacting efficiency, productivity, and profitability. With its application spanning various sectors, including electronics and 3D printing, understanding the intricacies of bulk material handling can provide businesses with the competitive edge they need. This comprehensive guide delves deep into what bulk material handling entails, its significance, and how companies like Polygonmach can leverage it to optimize operations.
Understanding Bulk Material Handling
Bulk material handling refers to the process of managing, transporting, and storing large quantities of materials in their raw or processed state. This discipline is vital in numerous industries, including manufacturing, mining, construction, and particularly in electronics and 3D printing, where precision and efficiency are paramount. The materials handled can range from grains and powders to metals and plastics, emphasizing the diversity and adaptability of this field.
The Importance of Bulk Material Handling in Modern Industries
In today's market, businesses are increasingly recognizing the benefits of effective bulk material handling systems. Here are some compelling reasons why:
- Increased Efficiency: Streamlined processes minimize delays and enhance workflow.
- Cost-Effectiveness: Reduced labor and operational costs significantly impact the bottom line.
- Safety Improvements: Automated systems reduce workplace accidents and improve employee welfare.
- Environmental Sustainability: Efficient handling lowers waste and optimizes resource usage.
Components of Bulk Material Handling Systems
Implementing an effective bulk material handling system involves several key components:
1. Conveyors
Conveyors are the backbone of any bulk material handling system. They transport materials across various distances and elevations, ensuring seamless movement from one point to another. Different types of conveyors, such as belt, screw, and roller conveyors, are utilized based on material type and operational requirements.
2. Hoppers and Silos
Hoppers and silos play a crucial role in the storage and dispensing of bulk materials. They help manage inventory levels and facilitate control over production processes. Proper design and maintenance of these units are essential to prevent blockages and ensure a steady flow of materials.
3. Feeders
Automatic feeders regulate the flow of materials into production equipment, providing a consistent supply and preventing bottlenecks. Proper sizing and calibration of feeders are critical to maintaining the desired production rate.
4. Dust Control Systems
Managing dust is essential for both operational efficiency and regulatory compliance. Dust control systems, such as dust collectors and suppressors, help maintain a clean work environment and ensure the safety of personnel.
5. Automation and Control Systems
Automation in bulk material handling enhances precision and reduces the potential for human error. Advanced control systems allow for real-time monitoring and adjustments, ensuring optimal performance throughout the handling process.
Benefits of Optimizing Bulk Material Handling
Optimizing bulk material handling systems yields numerous benefits, particularly in the electronics and 3D printing industries:
1. Enhanced Production Rates
Efficient material handling translates to higher production rates. With a streamlined approach, manufacturers can respond to market demands more rapidly, ensuring they are never short on stock.
2. Better Quality Control
When materials are handled properly, the risk of contamination and damage decreases. This is particularly critical in sectors like electronics, where product integrity is paramount.
3. Flexibility and Scalability
As businesses grow, their material handling needs may change. A robust bulk material handling system allows for easy scalability, enabling companies to expand operations without overhauling existing processes.
4. Improved Inventory Management
Effective bulk material handling systems facilitate better inventory tracking and management. This ensures that raw materials are available when needed, leading to reduced downtime and improved operational flow.
Challenges in Bulk Material Handling
Despite its numerous advantages, several challenges come with bulk material handling:
1. Equipment Maintenance
Regular maintenance of handling equipment is crucial. Downtime due to equipment failure can have significant implications for production schedules.
2. Worker Training
Proper training for employees on equipment and safety protocols is essential. Inadequately trained staff can lead to accidents and operational inefficiencies.
3. Evolving Technologies
Staying current with technological advancements is vital. Companies must continually assess and upgrade their systems to remain competitive.
Implementing Effective Bulk Material Handling Solutions
To implement an effective bulk material handling system, businesses should consider the following steps:
1. Assess Material Types and Requirements
Understanding the specific materials being handled is crucial. Each type of material has unique handling characteristics that dictate the requirements of the system.
2. Evaluate Current Processes
Perform a thorough evaluation of existing handling processes to identify inefficiencies and areas for improvement. This may include performance metrics, flow patterns, and equipment functionality.
3. Design and Plan the Handling System
Design a customized handling system that addresses the unique needs of the business, incorporating elements such as automation and control systems where applicable.
4. Automate Where Necessary
Implementing automation technology can significantly enhance handling processes. Robots and automated guided vehicles (AGVs) are increasingly used in bulk material management.
5. Train Your Workforce
Invest in comprehensive training for employees to ensure they are equipped to operate new systems safely and effectively.
6. Monitor and Optimize
Once implemented, continuously monitor system performance and look for opportunities to optimize and improve efficiency.
Future Trends in Bulk Material Handling
The future of bulk material handling looks promising, with emerging technologies set to revolutionize the industry:
1. Smart Technology
The integration of IoT (Internet of Things) devices is expected to provide valuable insights and real-time data analytics. This data can help improve decision-making and system responsiveness.
2. Robotics and Automation
As technology advances, the use of robots for material handling tasks is expected to increase, leading to enhanced precision and reduced labor costs.
3. Green Solutions
With an increasing focus on sustainability, future material handling systems are likely to emphasize environmentally friendly practices, reducing waste and energy use.
4. Advanced Tracking Systems
Improved tracking technologies, such as RFID and GPS, will allow for more precise inventory management and logistics within the supply chain.
Conclusion
In conclusion, bulk material handling stands as a vital facet of modern industries, particularly within electronics and 3D printing sectors. By embracing effective handling systems, businesses can elevate their operational efficiency, reduce costs, and enhance safety. As technology continues to advance, proactive businesses must stay abreast of trends and innovations to fully capitalize on the benefits of optimized bulk material handling.
Companies like Polygonmach are paving the way in this arena, providing cutting-edge solutions tailored to meet the diverse needs of various industries. By focusing on bulk material handling, organizations can ensure they are not only competitive but also resilient in a rapidly changing market.