The Art and Science of Molding Plastics in Business
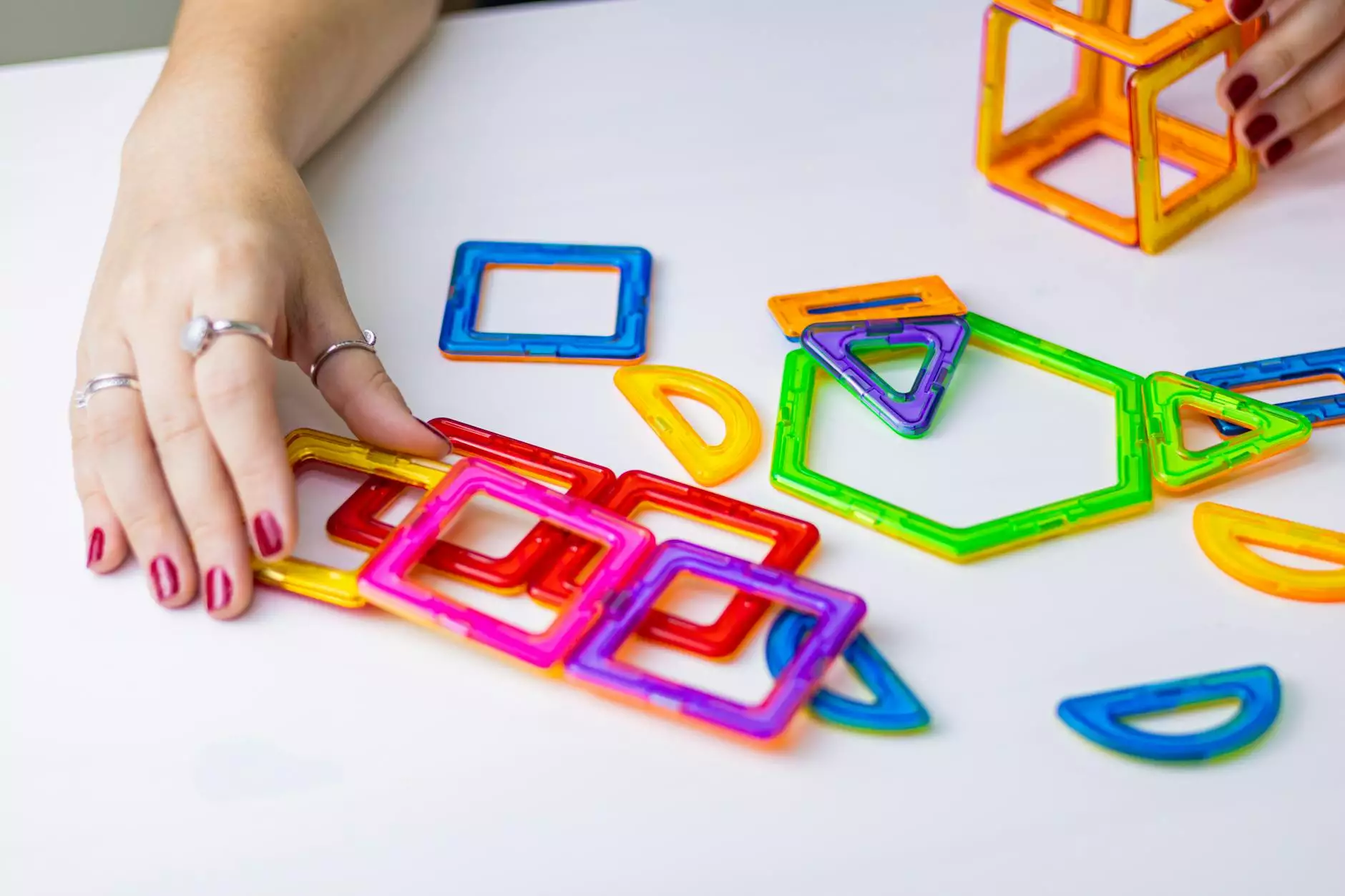
Molding plastics is a transformative technique that has revolutionized the manufacturing landscape, enabling businesses to create intricate designs with precision and efficiency. This article delves deep into the realm of molding plastics, highlighting its significance, applications, and its role in enhancing business success, particularly within the metal fabrication industry.
Understanding Molding Plastics
Molding plastics is a process that involves shaping materials through various techniques such as injection molding, blow molding, and rotational molding. Each technique has its own unique benefits and applications, making it essential for businesses to understand which method suits their needs best.
1. Injection Molding
Injection molding is one of the most popular techniques in the molding plastics sector. This process involves injecting molten plastic into a mold, where it cools and solidifies into the desired shape. Here are some key aspects of injection molding:
- High Efficiency: Capable of producing large volumes quickly.
- Precision: Excellent for creating complex shapes with tight tolerances.
- Material Variety: Compatible with a wide range of thermoplastics and thermosetting plastics.
2. Blow Molding
Blow molding, on the other hand, is employed to produce hollow plastic parts, such as bottles and containers. This method uses air pressure to expand heated plastic into a mold. Key points include:
- Cost-Effectiveness: Ideal for mass production of hollow items.
- Lightweight Products: Reduces material usage while maintaining strength.
- Custom Shapes: Capable of creating unique designs that cater to various industries.
3. Rotational Molding
Rotational molding is less common but serves a critical function in specific applications where large, hollow parts are required. The process involves placing plastic powder in a mold and rotating it in an oven, allowing the material to coat the interior surface evenly. Its advantages include:
- Uniform Thickness: Allows for a consistent wall thickness across the product.
- Durable Products: Produces items that can withstand tough conditions.
- Low Tooling Costs: More economical for low-volume production compared to other methods.
The Role of Molding Plastics in Metal Fabrication
For businesses involved in metal fabrication, integrating molding plastics can enhance capabilities and broaden service offerings. Here’s how:
1. Enhanced Design Capabilities
Molding plastics allows metal fabricators to incorporate complex plastic components into their designs, resulting in hybrid products that leverage the strength of metal with the versatility of plastic. This synergy enhances product design and functionality.
2. Cost Reduction
By substituting metal with molded plastic parts in certain applications, companies can significantly reduce material and energy costs. The lighter weight of plastic also leads to lower shipping costs and easier handling, contributing to overall savings.
3. Increased Production Speed
The efficiency of molding plastics allows businesses to speed up production processes, ensuring timely delivery of products to clients. This enhances customer satisfaction and can lead to increased business opportunities.
Key Benefits of Molding Plastics for Businesses
The incorporation of molding plastics into business operations comes with various advantages:
1. Versatility
Plastic can be molded into virtually any shape, providing businesses with the flexibility to innovate and meet diverse client needs. This adaptability is crucial in industries ranging from automotive to consumer goods.
2. Lightweight Enhancements
The lightweight nature of plastics over metals can lead to substantial benefits in industries where weight reduction is critical, such as aerospace and automotive. Products made from molded plastics are easier to transport and handle, greatly reducing overall costs.
3. Environmental Considerations
With increasing pressure on industries to adopt sustainable practices, molding plastics offers avenues for eco-friendliness. Many plastic materials are now recyclable, and innovations continue to bring biodegradable options to the forefront, promoting a circular economy.
Challenges in Molding Plastics
While the benefits are numerous, businesses must also be aware of challenges related to molding plastics:
1. Initial Investment Costs
The setup costs for molding machines and molds can be high. Businesses must assess their budget and forecast long-term returns on investment to justify these expenditures.
2. Material Limitations
Not all plastics are suitable for every application. Understanding the properties of various materials is crucial to ensure that the right type of plastic is used for specific products.
3. Process Limitations
Each molding method has its limitations regarding part size, complexity, and material compatibility. Businesses need to select the most appropriate method based on their project requirements.
Strategizing for Success in Molding Plastics
To capitalize on the opportunities presented by molding plastics, businesses should consider the following strategies:
1. Invest in Technology
Staying updated with the latest molding technologies can provide a competitive edge. Advanced machinery not only enhances production rates but also improves product quality and reduces waste.
2. Training and Development
Investing in workforce training ensures that employees understand the complexities of molding plastics and can operate machinery effectively. Continuous education keeps the workforce adaptable to future changes.
3. Focus on R&D
Research and development are critical for innovation. Companies should allocate resources to explore new materials and techniques to stay ahead in the market.
Conclusion: Molding Plastics as a Catalyst for Growth
In conclusion, the world of molding plastics is vast and full of potential. For businesses within the metal fabrication sector, embracing this technology can lead to improved product offerings, increased efficiency, and significant cost savings. As industries evolve, those who adapt and leverage the benefits of molding plastics will undoubtedly carve out a successful future.
For further exploration into how molding plastics can elevate your business, consider visiting DeepMould.net, where you can find additional resources and expert insights tailored for your industry needs.