Unlocking the Potential of Rapid Prototype Plastic Parts
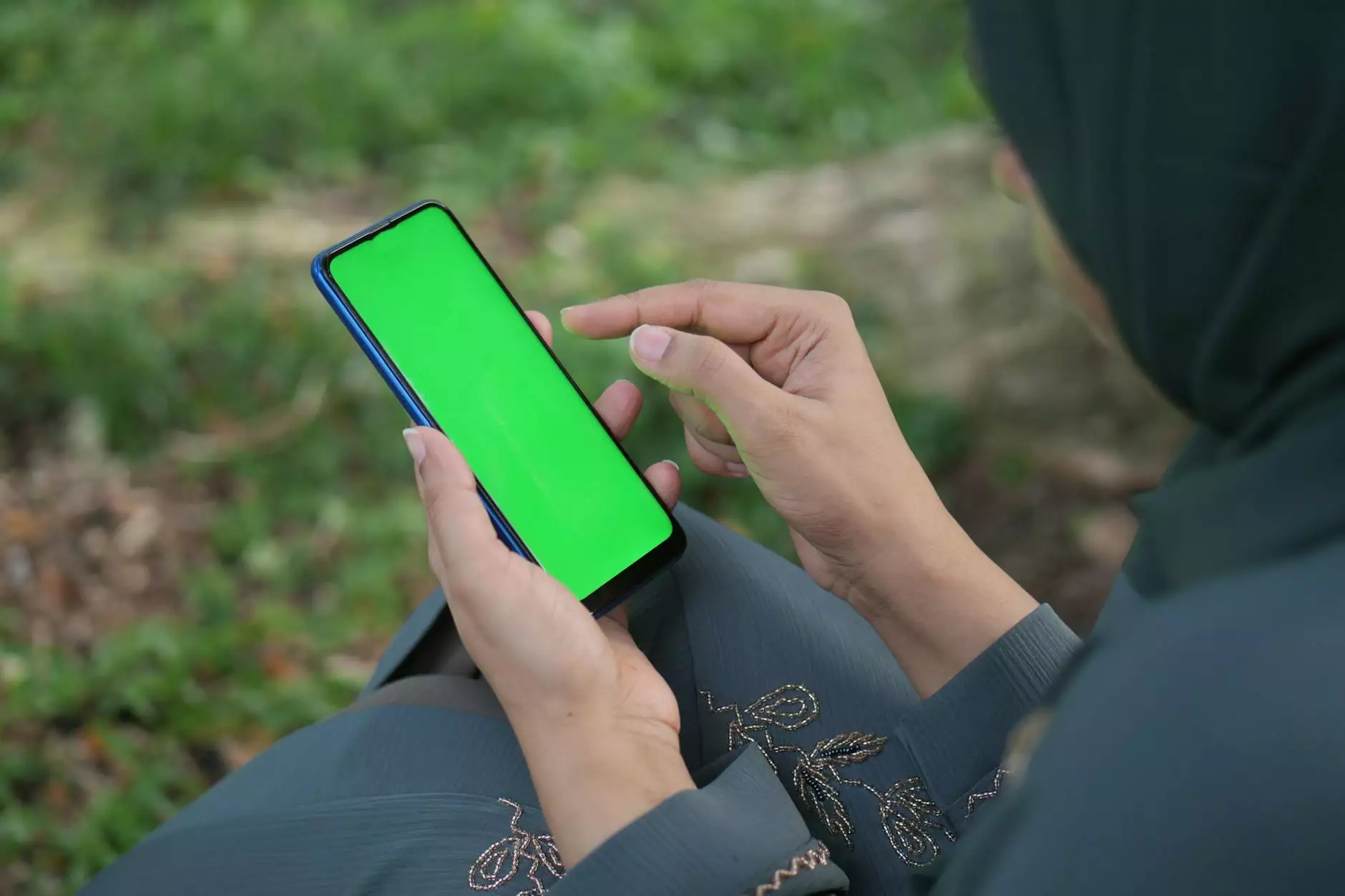
In today's fast-paced industrial landscape, businesses are constantly in search of ways to innovate and enhance their manufacturing processes. One of the most critical advancements in manufacturing is the ability to create rapid prototype plastic parts. This cutting-edge technology has revolutionized how products are developed, enabling companies to bring their ideas to life faster and more efficiently than ever before. In this article, we will dive deep into the world of rapid prototyping, explore its benefits, applications, and the significant role it plays in the realm of metal fabrication.
Understanding Rapid Prototyping
Rapid prototyping is a process that allows for the quick fabrication of physical parts using computer-aided design (CAD) data. The process can involve various techniques, including 3D printing, CNC machining, and injection molding. By employing these methods, manufacturers can expedite the design iteration process, allowing for swift modifications based on testing and feedback.
Benefits of Rapid Prototype Plastic Parts
There are numerous advantages to utilizing rapid prototype plastic parts in the manufacturing process. Here are some key benefits:
- Speed: Rapid prototyping significantly reduces the time required to produce parts, allowing companies to accelerate their product development cycles.
- Cost-Effectiveness: Rapid prototyping minimizes material waste and lowers the overall costs associated with product development.
- Flexibility: Designers can easily make changes to prototypes, ensuring that their final products meet design specifications without a lengthy revision process.
- Enhanced Communication: Physical prototypes serve as a tangible representation of ideas, facilitating better communication among stakeholders.
- Testing and Validation: Rapid prototyping allows for the early testing of products, aiding in the identification of potential design flaws before mass production.
Applications of Rapid Prototype Plastic Parts
The versatility of rapid prototyping means it can be applied across various industries. Here are some specific applications where rapid prototype plastic parts are making significant impacts:
1. Automotive Industry
The automotive sector frequently uses rapid prototyping to design and test components before they go into full-scale production. By creating plastic prototypes of parts, manufacturers can evaluate fit, function, and aesthetics, ultimately leading to safer and more efficient vehicles.
2. Aerospace Manufacturing
In aerospace, the need for lightweight and durable components is paramount. Rapid prototyping allows for the production of intricate shapes and structures that can withstand extreme conditions, ultimately enhancing the performance and safety of aircraft.
3. Consumer Goods Design
Consumer product manufacturers benefit particularly from rapid prototyping as it enables them to test product ergonomics and usability quickly. This process leads to more user-friendly designs and can result in higher customer satisfaction post-launch.
4. Medical Devices
In the medical field, rapid prototyping is essential for developing custom medical devices and surgical instruments tailored to individual patient needs. This personalization can significantly improve patient outcomes and recovery times.
The Role of Metal Fabricators in Rapid Prototyping
Metal fabricators are crucial players in the ecosystem of rapid prototype plastic parts. Their expertise in metal forming and fabrication complements the plastic prototyping process, providing an essential service that supports the development of hybrid products that combine both materials. Here’s how they contribute:
Material Selection and Combination
Metal fabricators assist in selecting the right materials to complement rapid prototype plastic parts, whether it involves integrating metal components within plastic designs or fabricating tooling used for injection molding.
Precision and Accuracy
With their advanced machinery and skilled workforce, metal fabricators ensure that the integration of metal and plastic components adheres to strict tolerances, enhancing the overall quality of the prototypes.
Scalability for Production
Once a prototype has been tested and refined, metal fabricators can scale the production process, ensuring that both plastic and metal parts can be produced efficiently and at the required volume.
Choosing the Right Partner for Rapid Prototyping
When it comes to selecting a partner for rapid prototype plastic parts, there are several factors to consider:
- Experience and Expertise: Look for a partner with a proven track record in rapid prototyping and a deep understanding of materials and methods.
- Technology and Equipment: Ensure that the partner uses the latest technologies and machinery to produce high-quality prototypes.
- Customer Service: A responsive and communicative partner can facilitate a smoother prototyping process and address any concerns that may arise.
- Portfolio and Case Studies: Reviewing previous work will give insights into the quality and capabilities of the potential partner.
The Future of Rapid Prototype Plastic Parts
The future of rapid prototype plastic parts looks promising as technology continues to evolve. Emerging trends include:
1. Advancements in 3D Printing Technologies
As 3D printing technology matures, we can expect higher precision, new materials, and faster printing speeds, enabling even more complex designs and faster turnarounds.
2. Integration of AI in Design Processes
Artificial intelligence will likely play a significant role in streamlining the design process, helping engineers predict potential issues and optimize designs in real-time.
3. Sustainability Initiatives
As the world shifts towards more sustainable practices, there will be an increased emphasis on using biodegradable materials in rapid prototyping processes, minimizing environmental impact.
Conclusion
The capability to produce rapid prototype plastic parts is a game-changer in the manufacturing landscape, offering unmatched speed, efficiency, and flexibility. As industries continue to adopt and refine these practices, the evolution of these technologies will usher in new opportunities for innovation and excellence in product development. By partnering with skilled metal fabricators and leveraging the latest advancements, companies can not only meet the demands of the market but also exceed customer expectations, paving the way for future success.
Call to Action
Are you ready to transform your product development process? Contact DeepMould.net today to learn more about how we can help you build high-quality rapid prototype plastic parts tailored to your needs. Let us help you innovate and accelerate your journey to market.